Understanding Plastic Injection Molding: The Future of Manufacturing
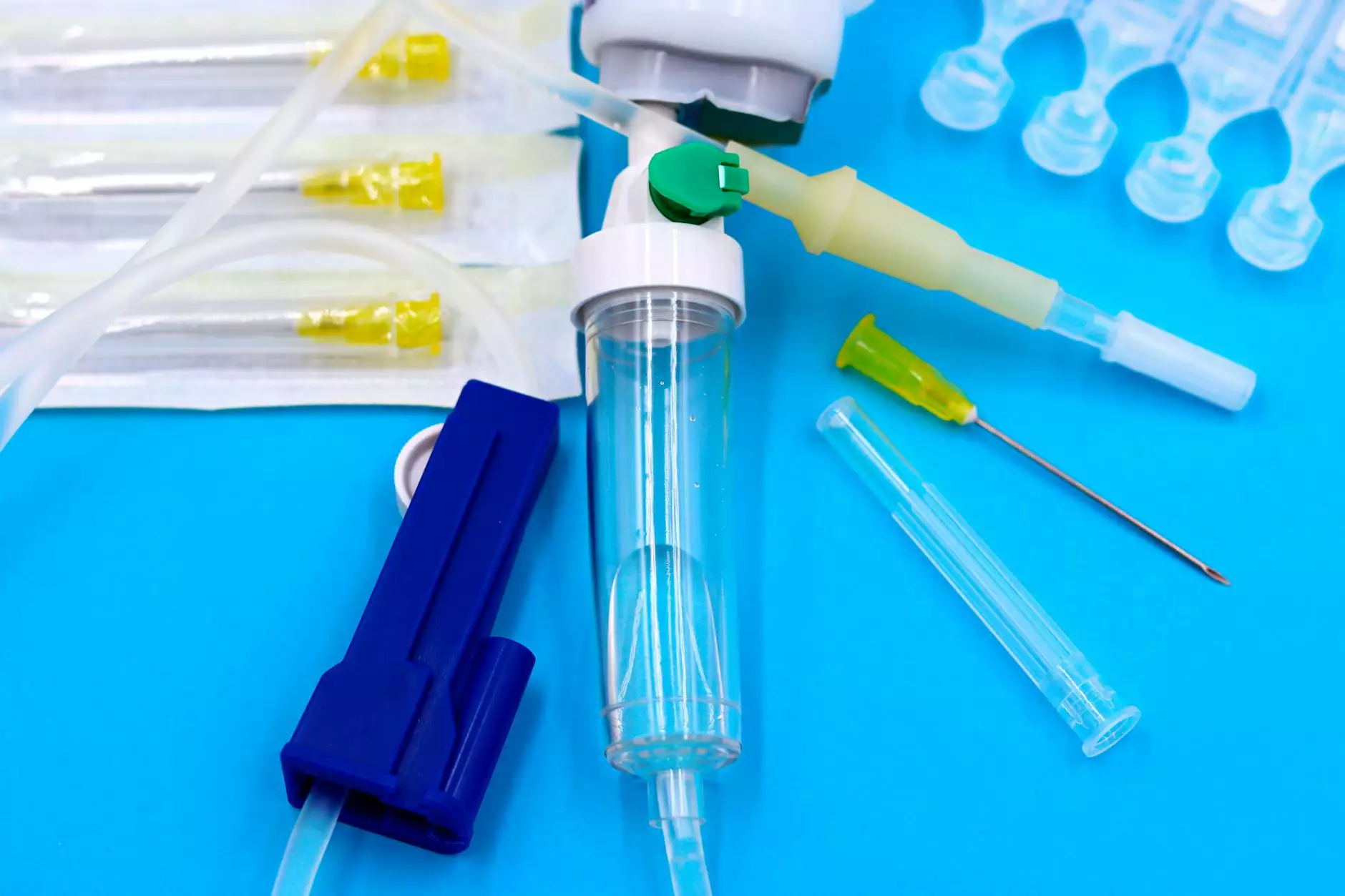
Plastic injection molding has become one of the most significant manufacturing processes in the modern industry. This technique allows for the mass production of various plastic products, leading to incredible advancements in efficiency, cost-effectiveness, and product quality. In this article, we will explore the intricacies of plastic injection molding, its applications, advantages, and why businesses like DeepMould are at the forefront of this technology.
What is Plastic Injection Molding?
Plastic injection molding is a manufacturing process that involves injecting molten plastic into a mold to create specific shapes and forms. It is widely used due to its ability to produce high volumes of parts with precision and efficiency. The process is highly automated and capable of producing complex designs, making it ideal for various industries.
How Does the Process Work?
The plastic injection molding process can be broken down into several key steps:
- Material Preparation: The process begins with the selection of plastic pellets, typically made from thermoplastics or thermosetting polymers. These pellets are fed into a hopper.
- Melting: The plastic pellets are heated to a molten state in a barrel using a combination of heat and pressure.
- Injection: The molten plastic is injected into a mold cavity through a nozzle. The mold is usually made of high-quality steel or aluminum and is designed to create the desired part shape.
- Cooling: Once the mold is filled, the plastic is allowed to cool and solidify, taking the shape of the mold.
- Ejection: After cooling, the mold opens, and the finished part is ejected. This cycle can take from a few seconds to several minutes, depending on the size and complexity of the part.
Applications of Plastic Injection Molding
The versatility of plastic injection molding makes it applicable across a variety of industries, including:
- Automotive: Used for dashboards, door panels, and various components due to its durability and lightweight properties.
- Consumer Products: From toys to kitchenware, the consumer market benefits significantly from the aesthetic appeal and intricate designs possible with injection molding.
- Medical Devices: Precision parts used in diagnostic equipment and surgical instruments are often produced with this method for its reliability.
- Electronics: Housings and components for gadgets often utilize plastic injection molding for detailing and precise fitting.
Advantages of Plastic Injection Molding
The benefits of utilizing plastic injection molding are numerous, including:
- High Efficiency: One of the most notable advantages is the speed of the production process, allowing for rapid turnaround times.
- Cost-Effectiveness: After the initial investment in molds, the cost per unit decreases significantly with larger production runs.
- Complex Geometries: Designers can create intricate details and complex shapes that would be difficult or impossible to achieve through traditional methods.
- Consistent Quality: High precision and consistency throughout production, ensuring each part meets defined tolerances.
- Diverse Material Choices: A wide range of plastics can be used, allowing for tailored properties (like flexibility, strength, and temperature resistance).
Choosing the Right Plastic Injection Molder
When selecting a plastic injection molder, businesses should consider several factors to ensure optimal results:
Experience and Expertise
Look for companies that have a proven track record in the industry. Experienced molders will understand the nuances of various plastics and techniques necessary for successful outcomes.
Technological Capabilities
The right manufacturer should utilize state-of-the-art machinery, enabling higher precision and efficiency. Advanced technology can significantly affect production speed and quality.
Quality Assurance Processes
Seek out molders that have rigorous quality control measures in place. This includes regular testing and inspection of parts to maintain high standards.
Scalability
Your chosen molder should be capable of scaling production according to your requirements, from small runs to large volumes.
Environmental Considerations in Plastic Injection Molding
As sustainability becomes a growing concern across industries,塑料注射成型 also evolves. Many companies, including DeepMould, are focusing on using recycled materials and creating more energy-efficient processes.
Using Recycled Plastics
Integrating recycled plastics into production not only reduces waste but also lowers material costs and carbon emissions. Many companies are developing biodegradable plastics that maintain the benefits of traditional plastics.
Energy Efficiency
Improving energy efficiencies through modern machinery and processes is another significant focus. Energy-efficient machines help lower operational costs and the overall environmental footprint.
The Future of Plastic Injection Molding
With ongoing advancements in technology, including 3D printing and automation, the future of plastic injection molding looks promising. As these technologies converge, they may enable even more innovative applications and improvements in production capabilities.
Conclusion
In conclusion, plastic injection molding is a transformative process that continues to evolve and shape the manufacturing landscape. From its high efficiency and cost-effectiveness to its ability to produce intricate designs, the advantages it offers make it indispensable in various industries. Companies like DeepMould exemplify leadership in this field, highlighting the importance of expertise, quality assurance, and innovation in delivering exceptional products.
As businesses continue to seek solutions that balance quality with cost, plastic injection molding will remain a cornerstone of modern manufacturing, driving growth and innovation for years to come.