The Definitive Guide to Industrial Vacuum System Design
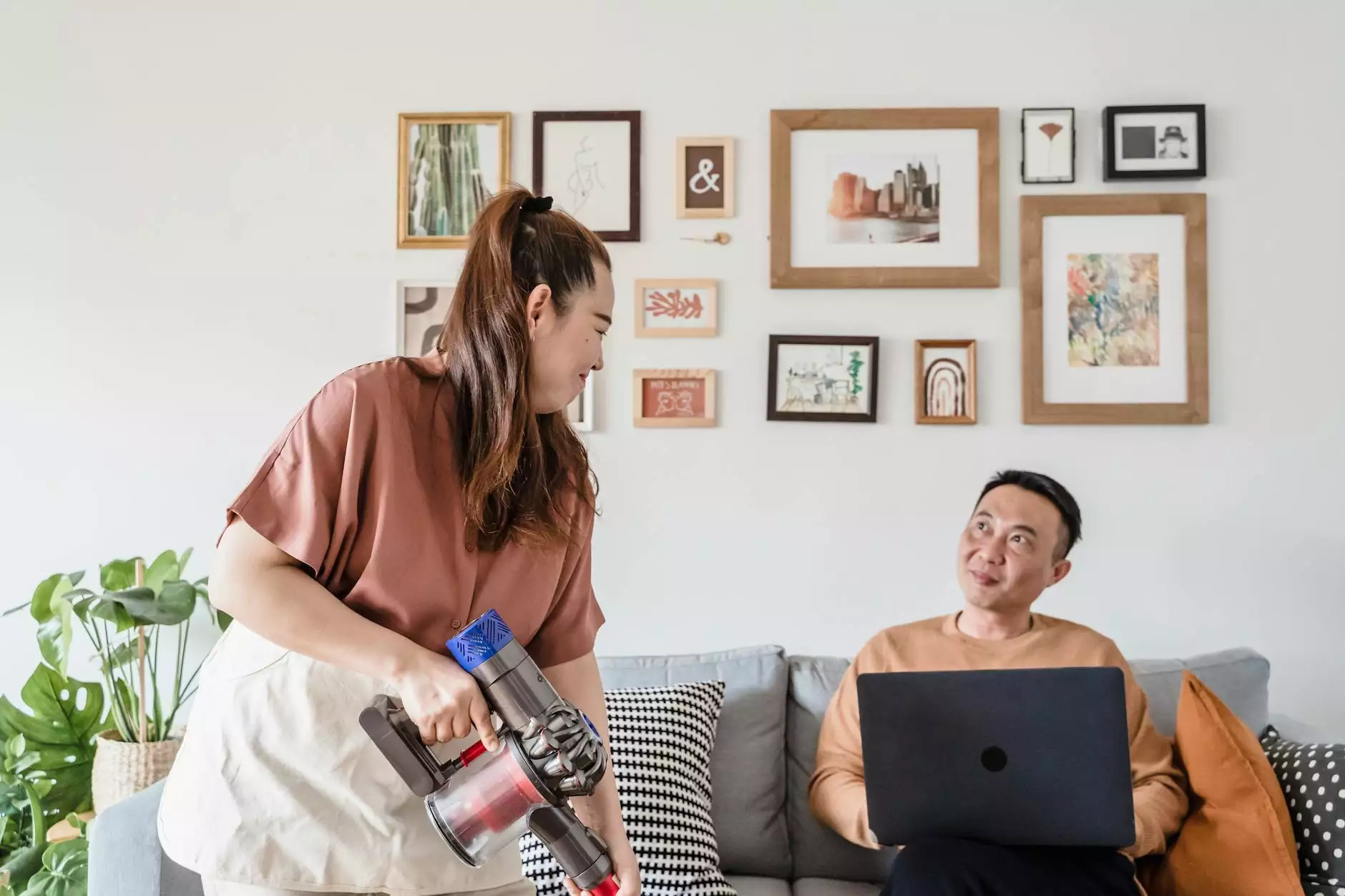
Understanding Industrial Vacuum Systems
Industrial vacuum systems are crucial for a myriad of industries, providing essential suction capabilities to maintain cleanliness and enhance operational efficiency. These systems are designed to manage a wide range of materials, from dust and debris to hazardous substances. Proper industrial vacuum system design can significantly reduce downtime and improve workplace safety.
Key Components of Industrial Vacuum Systems
A well-designed industrial vacuum system typically consists of several integral components, including:
- Vacuum Pump: The heart of the system, responsible for generating suction.
- Filtration System: Essential for trapping particles and maintaining air quality.
- Hoses and Attachments: Allow flexibility and reach to various areas.
- Collection Tank: Where the materials are accumulated for disposal or recycling.
- Control System: Manages the operation and efficiency of the vacuum system.
Benefits of Effective Industrial Vacuum System Design
Investing in a quality-designed vacuum system yields numerous advantages:
- Enhanced Safety: Reducing dust and contaminants decreases the likelihood of workplace accidents.
- Improved Efficiency: Automated systems can operate continuously, minimizing manual labor.
- Cost Savings: Streamlining processes and reducing downtime can significantly cut operational costs.
- Compliance: Adhering to safety regulations and environmental standards is easier with efficient systems.
Factors to Consider When Designing an Industrial Vacuum System
Designing an industrial vacuum system is not a one-size-fits-all approach. Several factors must be taken into account to ensure optimal performance:
1. Type of Material
The type of material being collected (e.g., dry, wet, hazardous) will impact the selection of equipment and materials.
2. Application Specifics
Different applications may require specific configurations and features, such as static controls or vacuum strength.
3. Space Constraints
The physical layout of the workspace can dictate the size and type of vacuum system needed. Compact designs may be necessary for small areas.
4. Noise Levels
It's important to consider noise pollution; quieter models may be preferred in environments where noise could disrupt workflow.
Applications of Industrial Vacuum Systems
Industrial vacuum systems find applications in various sectors. Here are some notable examples:
- Manufacturing: Ensuring clean production lines and preventing material contamination.
- Construction: Removing dust and debris for a safer work environment.
- Food Processing: Maintaining hygiene standards to avoid contamination.
- Medical Facilities: Critical for cleanliness and safety during procedures.
- Research Laboratories: Important for maintaining a clean and controlled environment.
Innovations in Industrial Vacuum System Design
Recent advancements have revolutionized the field of industrial vacuum systems. Some current trends include:
1. Smart Technology Integration
The integration of smart technology allows for real-time monitoring and adjustments within vacuum systems, enhancing overall efficiency.
2. Energy Efficiency
New designs focus on reducing energy consumption, aligning with global sustainability efforts and lowering operational costs.
3. Modular Systems
Modular vacuum systems provide flexibility, allowing companies to scale their operations as needed without a complete overhaul.
4. Advanced Filtration Techniques
Improvements in filtration lead to enhanced air quality, capturing smaller particles that traditional systems might miss.
Best Practices for Maintenance of Industrial Vacuum Systems
Maintaining your industrial vacuum system is crucial for longevity and performance. Here are some best practices:
- Regular Inspections: Conduct routine checks to identify and rectify any potential issues.
- Filter Changes: Replace filters as needed to ensure optimal air quality and efficiency.
- Scheduled Maintenance: Implement a proactive maintenance schedule to avoid unexpected breakdowns.
- Operator Training: Ensure that all operators are trained on the proper use and care of the vacuum system.
Case Studies: Success Stories from Various Industries
To understand the impact of effective industrial vacuum system design, let's look at a few case studies:
Case Study 1: Manufacturing Facility
A leading manufacturing facility revamped their vacuum system, leading to a 30% increase in productivity due to reduced downtime. Their new system effectively managed waste materials, enhancing safety and compliance.
Case Study 2: Food Processing Plant
A food processing plant implemented an advanced vacuum system with improved filtration. This not only met stringent health regulations but also improved product quality, resulting in higher customer satisfaction.
Case Study 3: Construction Site
By adopting portable vacuum systems, a construction company significantly decreased cleanup times and improved safety metrics on-site, thus winning more contracts due to their enhanced reputation.
Conclusion
In conclusion, understanding industrial vacuum system design is crucial for businesses across various sectors. By embracing best practices, staying updated on innovations, and tailoring systems to specific needs, companies can enhance safety, efficiency, and productivity. Investing in a well-designed vacuum system not only streamlines operations but also contributes to a cleaner, safer working environment.
For further insights and professional services, consider reaching out to experts in the field. Embrace the power of proper industrial vacuum systems and watch your business thrive.