Revolutionizing Medical Devices Manufacturing: The Impact of Radiation Shielding Materials
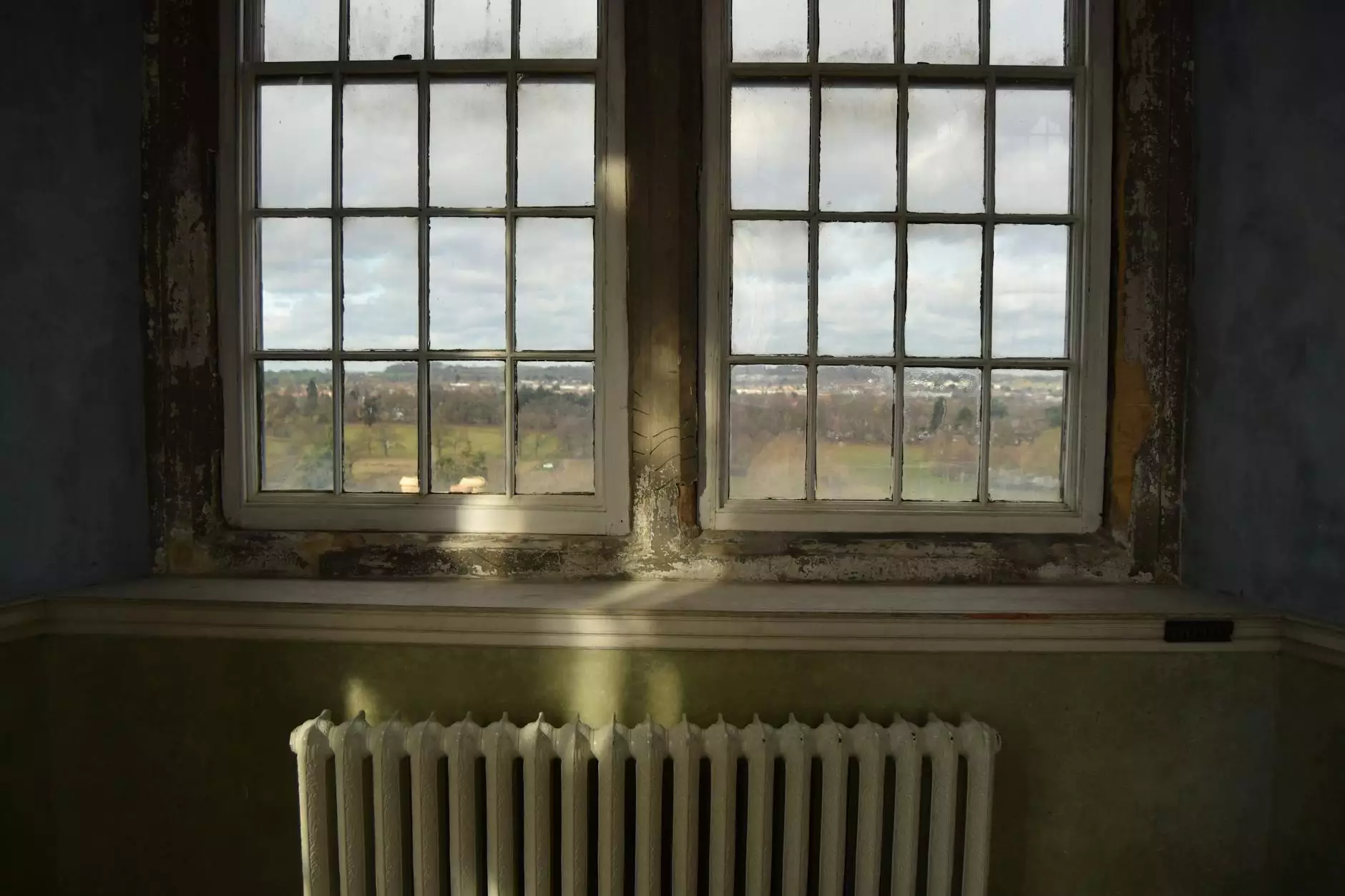
In today’s rapidly evolving healthcare landscape, the significance of medical devices manufacturing cannot be overstated. As technology advances, the demand for innovative solutions that enhance patient safety and efficacy in treatment has surged. Among the multitude of devices that are critical to modern medicine, the role of radiation shielding materials and devices stands out as particularly vital.
Understanding the Basics of Medical Devices Manufacturing
At its core, medical devices manufacturing encompasses the development and production of instruments, apparatuses, machines, implants, and in vitro reagents that assist in medical purposes, from diagnosis to treatment. The industry is not only about creating devices; it’s about creating solutions that improve the quality of life for patients.
The Importance of Quality in Medical Device Manufacturing
The medical devices industry is held to stringent regulatory standards. Manufacturers must adhere to guidelines set by health authorities like the FDA (Food and Drug Administration) and ISO (International Organization for Standardization). Quality assurance is paramount; thus, every step in the manufacturing process, from inception to delivery, requires meticulous attention to detail.
Focus on Radiation Shielding: A Critical Aspect of Medical Device Safety
Within the realm of medical devices, radiation shielding is essential. As medical imaging technology, such as X-rays and CT scans, becomes more prevalent, the potential for radiation exposure to both patients and healthcare professionals increases. This underscores the need for effective radiation shielding materials and devices.
What are Radiation Shielding Materials?
Radiation shielding materials are specifically designed to protect individuals from harmful radiation exposure. They are used in various applications, including hospitals, clinics, and diagnostic imaging centers. Common materials used in radiation shielding include:
- Lead: One of the most effective shielding materials due to its density.
- Concrete: Utilized in the construction of facilities that require radiation protection.
- Polyethylene: Effective for low-energy radiation and neutron shielding.
- Specialty Composites: Innovatively engineered materials tailored for specific shielding requirements.
Innovations in Radiation Shielding Devices
The advancement in technology has led to the development of various radiation shielding devices that enhance protection without compromising the quality of care. Some innovative devices in the market include:
Radiation Shielding Aprons
These protective garments are essential for healthcare professionals working in radiology departments. Made from layered composite materials, they provide flexibility and mobility while ensuring safety from scattered radiation.
Lead-lined Walls and Barriers
The installation of lead-lined walls in imaging rooms is a crucial architectural consideration in medical facilities. These barriers ensure that radiation does not leak into adjacent areas, protecting patients and staff alike.
Mobile Radiation Shielding Solutions
Portable shielding solutions are increasingly in demand for their versatility. Mobile radiation shielding devices can easily be repositioned to offer protection wherever necessary, making them invaluable in various clinical settings.
The Manufacturing Process of Radiation Shielding Devices
Manufacturing radiation shielding devices involves several key steps:
- Design and Engineering: Advanced software is utilized to model and simulate the effectiveness of shielding materials.
- Material Selection: The choice of shielding materials is critical; manufacturers must consider factors such as weight, flexibility, and radiation attenuation properties.
- Production: Precision machining and crafting techniques are employed to produce high-quality shielding devices.
- Quality Control: Rigorous testing ensures that the final products meet regulatory standards and perform as intended.
Challenges in Medical Devices Manufacturing
The road to innovation in medical devices manufacturing is not without challenges. Some of the key hurdles include:
- Regulatory Compliance: Navigating the complex regulations set forth by health authorities can be daunting for manufacturers.
- Cost Management: Keeping production costs low while maintaining high standards is a critical balancing act.
- Technological Advancements: Staying ahead of rapid technological changes requires ongoing investment in research and development.
Future Trends in Medical Devices Manufacturing
The future of medical devices manufacturing appears promising, driven by several key trends:
1. Integration of AI and Machine Learning
Artificial Intelligence (AI) and machine learning technologies are beginning to play a crucial role in the manufacturing process, improving efficiency and reducing human error. AI can help in predictive maintenance, quality assurance, and even in the design phase.
2. Advanced Materials Science
Research in materials science continues to unveil new opportunities for better performance. The development of materials that are lighter, stronger, and more effective at shielding could revolutionize the production of radiation shielding devices.
3. Sustainability in Manufacturing
As environmental concerns grow, manufacturers are increasingly focusing on sustainable practices. The adoption of green manufacturing techniques is becoming more common, ensuring that processes minimize waste and reduce energy consumption.
Conclusion: The Pivotal Role of Medical Devices Manufacturing in Healthcare
In conclusion, the landscape of medical devices manufacturing is ever-evolving, driven by innovation, regulatory demands, and the continuous quest for improved patient safety. The significance of radiation shielding materials and devices within this industry cannot be overstated. They are critical components in protecting lives while enabling healthcare professionals to deliver essential diagnostic and therapeutic services.
As we look towards the future, manufacturers like OVM Device are poised to lead the way in developing cutting-edge solutions that not only adhere to the highest standards of quality but also address the evolving needs of the healthcare sector.
Call to Action
For professionals interested in the advancements of medical devices manufacturing, especially in radiation shielding materials and devices, we invite you to explore our offerings at OVM Device. Together, let's create a safer and more efficient healthcare environment.