The Importance of Mold and Tooling in Modern Manufacturing
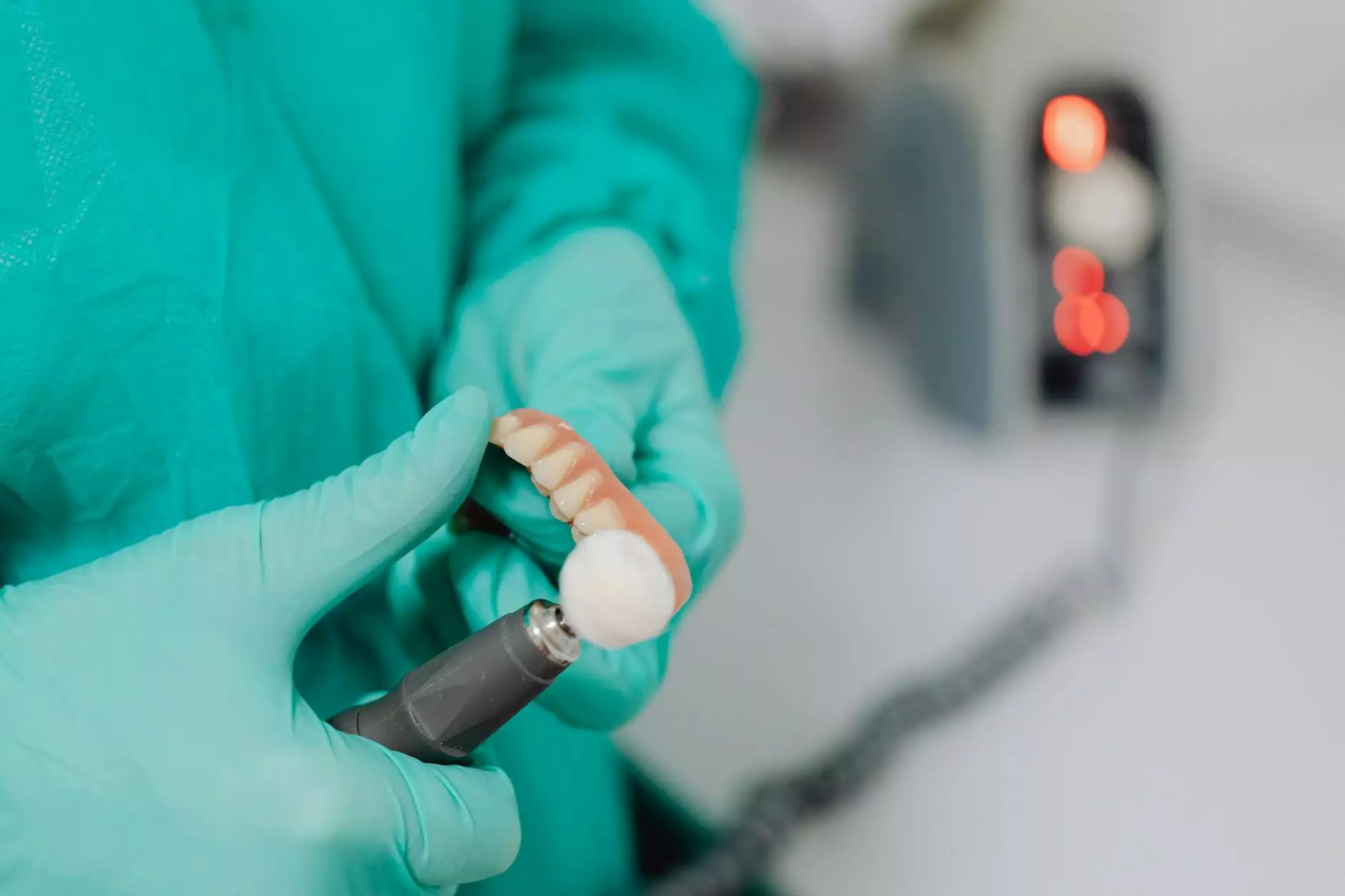
In the intricate landscape of manufacturing, the terms mold and tooling hold immense significance. These processes are not just technical terminology; they are at the heart of efficient production, cost-effectiveness, and ultimately, the success of manufacturing businesses, such as DeepMould. Understanding how mold and tooling influence manufacturing can empower organizations to enhance productivity and quality.
Understanding Mold and Tooling
To grasp the importance of mold and tooling, one must first understand what these terms encapsulate. Mold refers to a hollow form used to give shape to molten or hot liquid material, such as plastic, metal, or glass. Tooling encompasses a broader category that includes not only molds but also the various tools required to shape, cut, and finish materials during the manufacturing process.
The Integral Components of Mold and Tooling
The realm of mold and tooling involves several integral components:
- Molds: Custom-designed to meet specific product requirements.
- Toolkits: Essential for various manufacturing processes, including machining, casting, and forging.
- Machinery: Advanced devices that facilitate accurate and efficient production.
- CAD/CAM Technology: Software tools that enhance the design process and manufacturing precision.
The Relevance of Mold and Tooling in Metal Fabrication
Metal fabrication stands as one of the most critical arenas where mold and tooling play a pivotal role. Fabricating metal parts and structures necessitates precision and reliability, and the right mold and tooling can significantly enhance these traits.
1. Precision Engineering
In industries where every millimeter counts, the precision stemming from mold and tooling in metal fabrication cannot be overstated. Using advanced technology such as CNC machines ensures that metal parts are fabricated to exact specifications. This precision leads to higher quality products that meet stringent industry standards.
2. Cost Efficiency
Investing in high-quality molds and tools may require a significant upfront cost, but the return on investment is substantial. With the right mold and tooling, production times are reduced, and waste is minimized, leading to overall cost savings. Businesses in metal fabrication can produce items faster and with fewer materials wasted, ultimately increasing profit margins.
3. Versatility in Production
Modern manufacturing demands versatility. Molds that can produce various components without needing extensive retooling can save time and resources. When utilizing advanced tooling solutions, companies such as DeepMould can easily switch from one product to another, maintaining efficiency and meeting customer demands swiftly.
Types of Molds and Tools Used in Manufacturing
The manufacturing landscape incorporates various types of molds and tools based on specific applications. Understanding these can help businesses choose the right tools for their needs.
Injective Molds
These molds are widely used in the production of plastic components. Injection molding involves injecting molten material into a mold, allowing it to cool and solidify. It is particularly effective for high-volume production.
Compression Molds
Compression molds are used predominantly in producing rubber and some thermoset plastics. This involves placing material into an open, heated cavity; once closed, the mold reshapes the material into the desired part.
Blow Molds
Blow molding is used for producing hollow plastic parts. It is essential in manufacturing products like bottles and containers, showcasing the versatility of mold and tooling solutions.
Advancements in Mold and Tooling Technology
Technological advancements have dramatically transformed the fields of mold and tooling. Today, businesses leverage innovative technology to improve production efficiency, accuracy, and reliability:
1. 3D Printing in Tooling
3D printing, especially in creating molds, has revolutionized traditional manufacturing. This technology allows for rapid prototyping and the creation of complex mold designs that were previously impossible with conventional methods.
2. Smart Tools and Automation
Integrating IoT (Internet of Things) with manufacturing tools has paved the way for smart machinery that can monitor, adjust, and report on production processes in real-time. This intelligent integration bolsters efficiency and reduces the likelihood of human error.
3. Software Enhancements
Advanced CAD/CAM software assists businesses by simplifying the design and production planning phases. These tools help manufacturers visualize the end product and optimize the manufacturing process.
Choosing the Right Partner for Mold and Tooling Needs
As the demand for quality and efficiency increases, choosing the right partner for mold and tooling is crucial. When evaluating potential partners, consider the following criteria:
- Experience and Expertise: Look for a partner with a proven track record in the industry.
- Technology and Machinery: Ensure that they utilize state-of-the-art technology to produce high-quality molds and tools.
- Customization Capabilities: Your partner should be able to cater to specific needs and customize molds as necessary.
- Quality Assurance Processes: A partner with stringent quality checks will help ensure that the products meet all specifications.
Conclusion: The Future of Mold and Tooling in Manufacturing
The domain of mold and tooling continues to evolve. Companies must embrace the growing technological advancements and the shifting demands of the market. By partnering with competent providers like DeepMould, businesses in metal fabrication can ensure they stay ahead of the competition, produce high-quality products, and maintain cost-effectiveness.
As industries expand and diversify, the importance of effective mold and tooling practices becomes clearer. Investing in these areas today will yield substantial benefits in productivity, efficiency, and quality, paving the way for future success.
Contact Us
If you're interested in enhancing your manufacturing processes through superior mold and tooling solutions, visit DeepMould today. Our team of experts is ready to assist you in achieving your production goals with the highest standards of quality.