Expert Guide to H2S Monitor Calibration
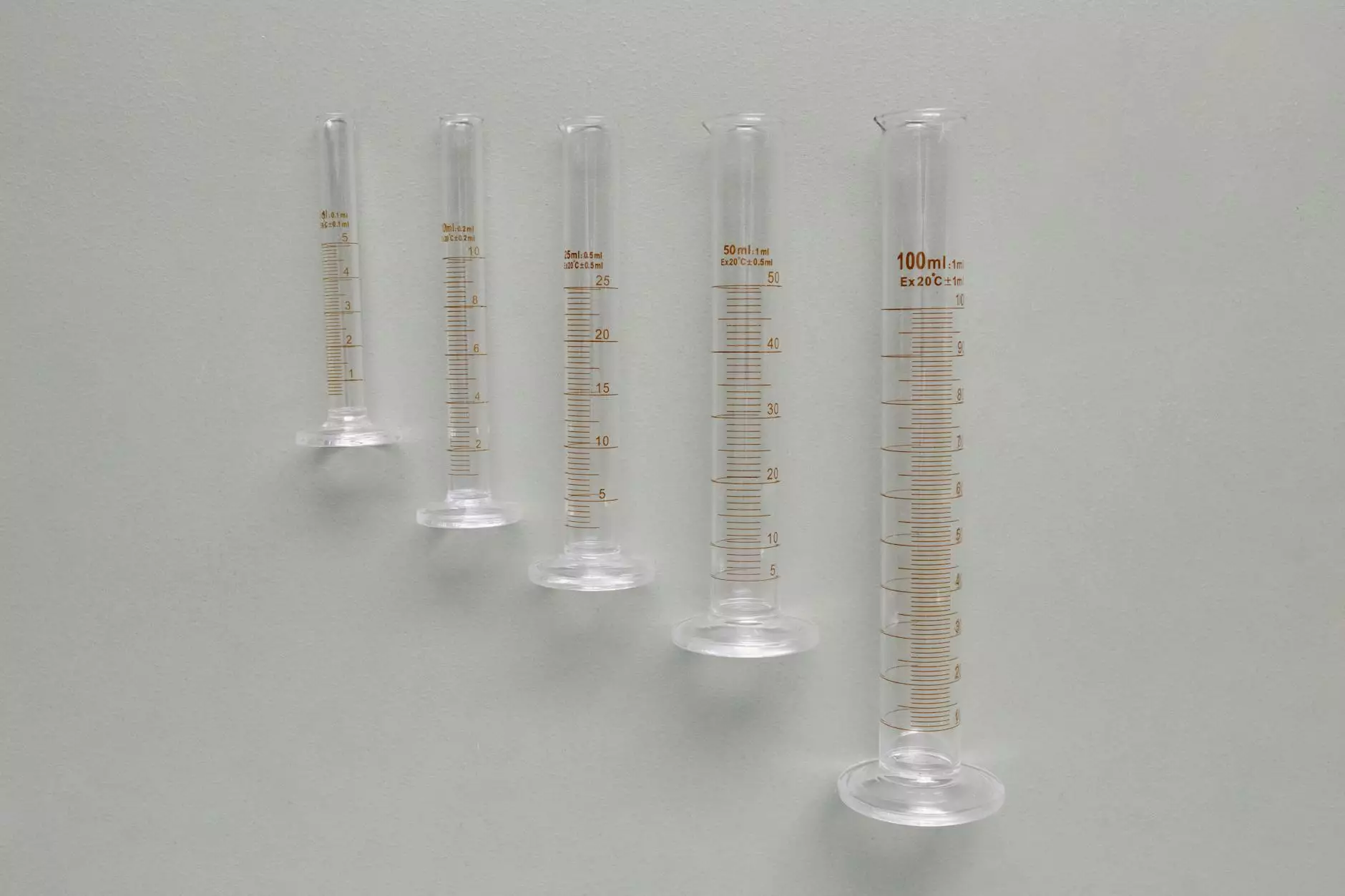
The calibration of H2S monitors is an essential process in maintaining safety standards in industries dealing with potentially hazardous gases. In this article, we will cover comprehensive details regarding the importance of H2S monitor calibration, its procedures, and best practices to ensure optimal functionality of your monitoring equipment.
Understanding H2S Monitors
Hydrogen Sulfide (H2S) is a highly toxic gas that poses serious health risks, including respiratory issues and even death. Thus, H2S monitors serve a crucial role in detecting and measuring this hazardous gas in the air. Proper calibration of these devices ensures that they provide accurate readings, which are vital for the safety of personnel and the environment.
Why is H2S Monitor Calibration Important?
Calibration is the process of configuring an instrument to provide a result for a sample within an acceptable range. Here are a few reasons why H2S monitor calibration is indispensable:
- Safety Assurance: Regular calibration confirms that your monitors are accurately detecting H2S levels, thus safeguarding workers’ health.
- Compliance with Regulations: Many industries are regulated by strict safety standards. Properly calibrated monitors are key to compliance.
- Optimal Performance: Calibration enhances the performance of H2S monitors, ensuring they function correctly in high-risk environments.
- Reduced False Alarms: Frequent calibration minimizes the chances of false readings, preventing unnecessary panic and disruptions.
When Should You Calibrate Your H2S Monitor?
Understanding when to perform calibration is pivotal. Consider the following guidelines:
- Before use: Always calibrate before you use the monitor for the first time.
- Monthly basis: For continuous use, a monthly calibration is recommended.
- After exposure to high concentrations: If the monitor has been exposed to high levels of H2S, recalibration is essential.
- Post-servicing: Any maintenance or service performed on the device should be followed by recalibration.
Steps to Properly Calibrate H2S Monitors
To ensure that your H2S monitor calibration is effective, follow these detailed steps:
1. Gather Necessary Equipment
Before starting calibration, ensure that you have access to:
- Calibration gas with a known concentration of H2S.
- Flow regulators.
- A suitable calibration adapter for your monitor.
- An instruction manual specific to your H2S monitor model.
2. Prepare Your Monitor
Turn off the H2S monitor and let it settle for a few minutes. This helps in stabilizing the readings for accurate calibration. Ensure that the device is clean and free from any obstructions.
3. Connect the Calibration Gas
Using an appropriate calibration adapter, connect your H2S monitor to the calibration gas cylinder. Be sure to follow safety protocols and wear the necessary PPE (personal protective equipment) during the process.
4. Adjust the Monitor
With the calibration gas flowing, allow the H2S monitor to read the gas concentration. Follow the manufacturer’s instructions on how to adjust the readings. Most monitors will require you to press a calibration button to set the current reading as the zero point.
5. Verify Calibration
After adjusting, disconnect the gas and allow the monitor to return to normal conditions. Test the monitor again with fresh air to verify that it reads zero. This step confirms that the calibration process was successful.
6. Document the Calibration
It’s essential to keep records of all calibration activities. Document the date, gas concentration used, and any adjustments made. This practice supports compliance and can be crucial in audits.
Best Practices for H2S Monitor Calibration
Adhering to best practices can enhance the accuracy and reliability of H2S monitors:
- Use approved calibration gas: Ensure that the gas used is from a reputable supplier and meets the required specifications for your monitor.
- Calibration in controlled environments: Perform calibration in a controlled environment to avoid external factors affecting the readings.
- Training and familiarization: Ensure all users are adequately trained and familiar with the specific monitors and calibration processes.
- Regular checks: Besides scheduled calibrations, perform regular checks on the monitor’s functionality to catch issues early.
Conclusion
In conclusion, H2S monitor calibration is a critical process for ensuring safety in workplaces exposed to hydrogen sulfide. By understanding the necessity, recognizing when to calibrate, following proper procedures, and adhering to best practices, organizations can significantly reduce risks associated with H2S exposure.
Investing in regular calibration and maintenance of H2S monitors not only protects personnel but also contributes to a safer workplace environment. For more educational resources on H2S monitors and safety training, visit H2S Online Training.